Acetal Plastic Injection Moulding
Stephens Plastic Mouldings Mouldings Limited has a large selection of injection moulders to meet your plastic moulding requirements. We’ve been in the plastic moulding business since January 2011, and we’ve served thousands of customers around Birmingham and the West Midlands. We have years of experience, creative and original ideas, and genuine passion. In addition, our objective is to provide the greatest plastic injection moulding to our faithful clients by utilising current machinery and the most up-to-date method. We use an array of materials for our injection moulding, one being Acetal.
Acetal Plastic Injection Moulding
Acetal materials are hard and tough. In addition, they are also resilient and offer high impact resistance at different temperatures, including very low ones. Out of these materials, homopolymers are characterised by the highest strength, and copolymers offer high thermal stability. These properties are taken into consideration when manufacturing items by means of acetal plastic injection moulding.
Homopolymers are used for items which will be used in the condition of high fatigue. This is because they have a high resistance to its impact, and they also have high tensile strength. Copolymers, on the other hand, are used for parts which will be subjected to hot water impact or alkalis impact, because they have a high resistance to such impacts.
- High termal stability
- Gears, bearings, valves etc
- Resistant to chemicals
- Years of moulding experience
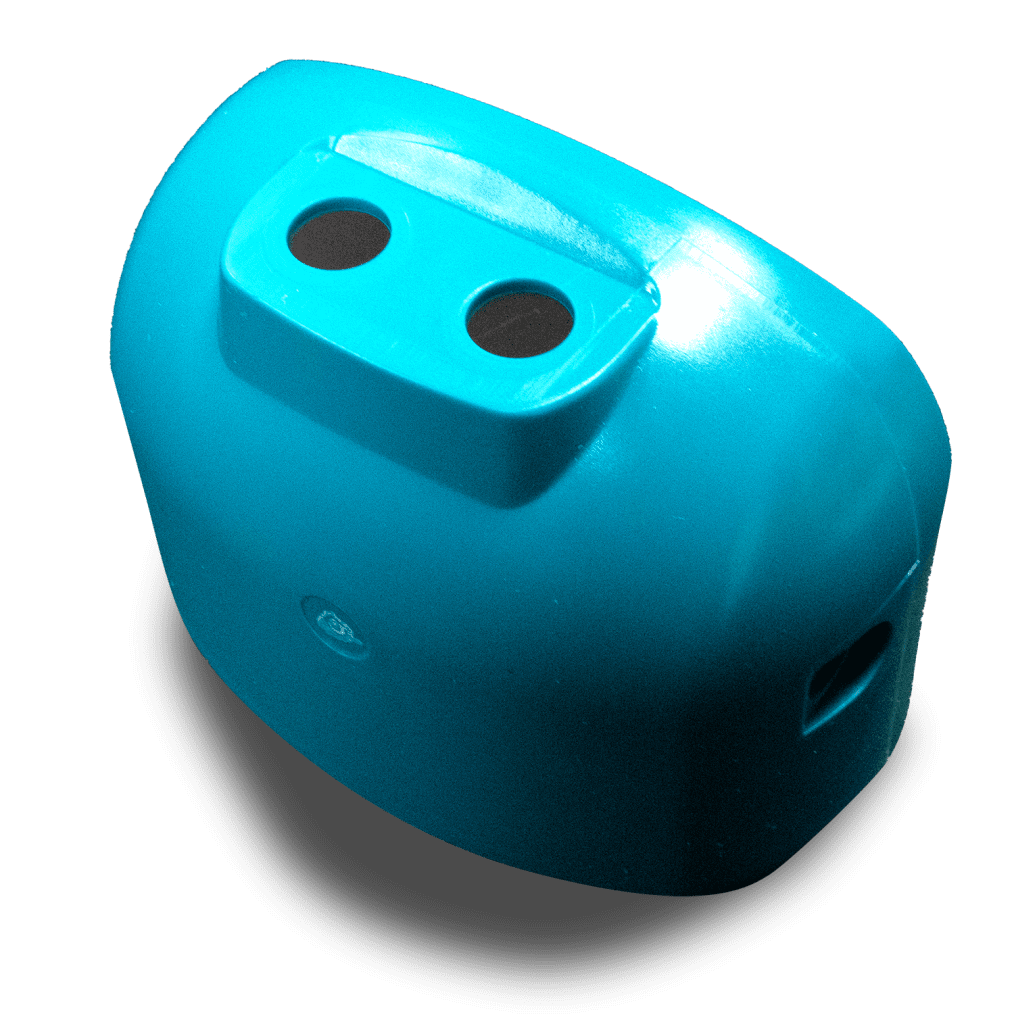
Acetal materials are processed easily by means of acetal plastic injection moulding. Because there are not many adhesives suitable to join acetal parts, joining is implemented by means of snap fit joints, by threading or riveting. In some cases people can choose to weld acetal parts ultrasonically.
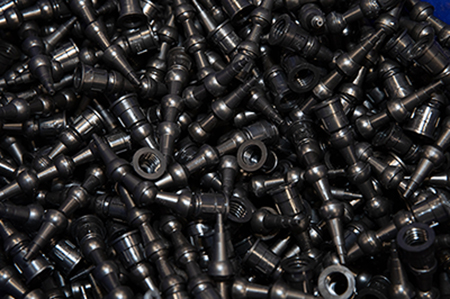
Parts which are made by the acetal plastic injection moulding method comprise of: gears, bearings, plumbing fittings, valve housings, pump housings, auto fuel system parts, etc. These are uses where the properties of this material are highly beneficial. For instance, toughness, resilience, and rewarding dimensional stability.
Furthermore, acetal is resistant to chemicals, and is especially resistant to alcohols and oils. It is also characterised by very low water absorption. All these qualities are important when choosing what parts to produce by acetal.
It should be noted that in the course of acetal plastic injection moulding, shrinkage cannot be uniform in all directions. So, round parts can become somewhat oval, and there can be some warpage of flat and thin walled parts. These peculiarities have to be taken into account during the design of parts to be made by acetal injection moulding, to obtain optimal parts.
We’d Love to Hear From You, Get In Touch With Us!
Please contact us if you would like to receive a quotation and/or to find our more about how we can provide the service you are looking for.